Six Degrees of Freedom
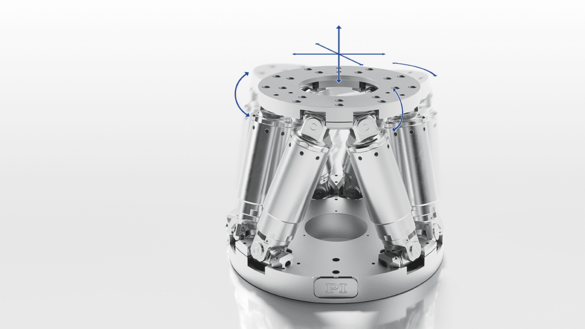
Six Degrees of Freedom
Precision hexapods enable motion in six degrees of freedom in only one mechanical structure. The platform moves in three translational axes (X, Y, Z) and three rotational axes (ΘX, ΘY, ΘZ). The typical parallel-kinematic structure of hexapods consists of six variable-length actuators, each of which is connected to a base plate and a movable platform via joints.
Compact Installation Space
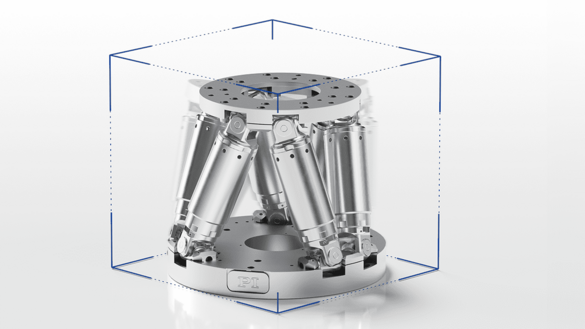
Compact Installation Space
Thanks to their parallel-kinematic design, hexapods can perform multi-axis movements, even in the most compact installation spaces. This allows them to be optimally integrated in custom processes, machines, and systems.
Freely Definable Center of Rotation
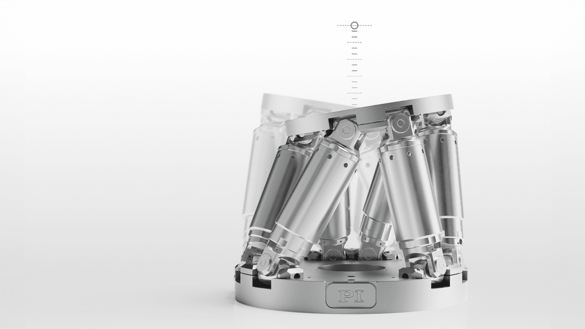
Freely Definable Center of Rotation
For precision hexapods from Physik Instrumente (PI), the center of rotation’s position (pivot point) and the orientation of the reference coordinate system can be defined quickly and easily using software commands. Within the coordinate systems, the freely selectable center of rotation offers maximum flexibility for precisely adapting the hexapod motion platform to specific requirements. The predefined work and tool coordinate systems can be activated or deactivated at any time. Changing the mechanical components is not required.
High Degree of Stiffness
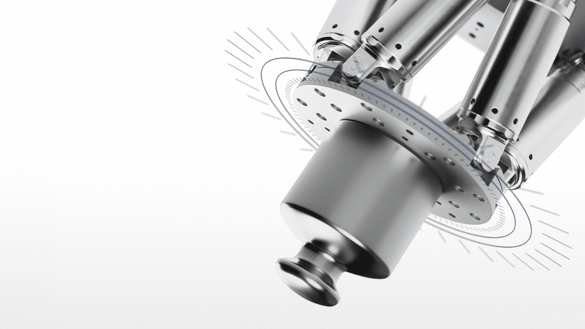
High Degree of Stiffness
Thanks to the parallel-kinematic design, hexapods are characterized by their high degree of stiffness. The performance of the hexapods is therefore not affected by external forces. They can maintain the required position even when subjected to variable forces.
Outstanding Tracking Accuracy and Dynamics
Outstanding Tracking Accuracy and Dynamics
The high dynamics of the system and a sophisticated controller allow for optimal alignment between target and actual position. Trajectories for sinusoidal oscillations can be achieved via the controller as required and allow motion sequences with maximum tracking accuracy. Moreover, dynamic movements and oscillations can be achieved with comparatively low energy consumption, as the actuators only move the platform and therefore little mass.
Easy Integration
The powerful hexapod controller guarantees simple, intuitive control of the parallel-kinematic systems: All target positions can be commanded in Cartesian coordinates. The controller performs calculations to control the actuators and the resulting desired motion of the platform. PI’s universal graphical user interface (GUI) can be used to control and start up not only all hexapod systems, but also all other PI positioning systems with any drive technology. An industrial EtherCAT interface is available for the integration in automation processes.
Discover the Wide Variety of PI Precision Hexapods
PI precision hexapods are based on more than three decades of experience in development and manufacturing. With its extensive portfolio of drive technologies—from piezoelectric to electromagnetic—PI offers hexapods in combination with exceptional sensor technology, software, and motion controllers for a wide variety of specification requirements and installation situations. Thanks to powerful, intuitive controllers and software, the hexapods can be easily and precisely controlled.
Discover the wide variety of PI precision hexapods for loads from 1 kg to 250 kg and repeatability to ±0.06 µm for standard versions. Custom precision hexapods for loads over 2,000 kg are also available.