In the case of PICMA® piezo actuators, the actual piezo ceramic is protected by an all-ceramic insulation layer against humidity and failure due to increased leakage current. The monolithic piezo ceramic block of a PICMA® actuator achieves excellent reliability, even under extreme ambient conditions, and thus extends the lifetime by several orders of magnitude.
Due to this inorganic, ceramic protective layer, the PICMA® multilayer actuators are proven to be considerably superior to polymer-insulated actuators. PICMA® multilayer piezo actuators are available in numerous designs with different >> displacement modes.
- Large temperature range
The particularly high Curie temperature of 320 °C enables a useable temperature range of up to 150 °C, well beyond the 80 °C limit of conventional multilayer actuators. PICMA® piezo actuators work at a reduced travel even in the cryogenic temperature range. - Optimal UHV compatibility
The exclusive use of inorganic materials, e.g., for insulation and electrical contact, provide the optimum conditions for use in ultra-high vacuum: No outgassing and high bakeout temperatures. - Neutral in magnetic fields
Every actuator is constructed exclusively of nonferromagnetic materials, giving them extremely low residual magnetism of the order of a few nanotesla.
The internal electrodes and the piezo ceramic are sintered together (cofiring technology) resulting in a monolithic piezoceramic block. The inorganic, ceramic insulation layer prevents the penetration of water molecules and thus extends the lifetime by several orders of magnitude when compared with merely polymer-coated multilayer actuators (Fig. 2). At the same time the sensitive internal electrodes are protected reliably against mechanical damage and soiling.
Reducing Mechanical Tension
Slots on the side of the PICMA® actuators effectively prevent excessive mechanical tensile stress in the passive regions of the stack and the formation of uncontrolled expansion cracks, that may lead to electrical breakdowns causing damage to the actuator (Fig. 3).
The meander-shaped design of the external contact strips ensures stable electrical contact with all inner electrodes, even under extreme dynamic loads (Fig. 4).
Lifetime at DC Operation
In nanopositioning applications, constant voltages are usually applied to the piezo actuator for extended periods of time. In the DC operating mode, the lifetime is influenced mainly by atmospheric humidity. If the humidity and voltage values are very high, chemical reactions can occur and release hydrogen molecules which then destroy the ceramic composite by embrittling it.
In elaborate tests, a model was developed to calculate the lifetime of the PICMA® stack actuators. The following factors had to be taken into account under concrete conditions of application: The ambient temperature, the relative humidity and the level of applied voltage.
This simple formula allows a quick estimation of the average lifetime in hours:
With decreasing voltage values the lifetime increases exponentially. For example, the expected lifetime at 80 V (DC) is ten times as high as with 100 V (DC).
This calculation can also be used to optimize a new application with regard to lifetime already in the design phase. A decrease in the driving voltage or control of temperature and atmospheric humidity by protective air or encapsulation of the actuator can be very important in this regard.
The following values can be read from the diagram for continuous operation at 100 VDC with 75 % relative humidity (RH) and an ambient temperature of 45 °C:
- AU = 75 (black curve)
- AT = 100 (red curve)
- AF = 14 (blue curve)
The product has an average lifetime of 105,000 h, in other words, more than 11 years.
Accelerated Lifetime Test under Quasi-Static Conditions
Their high reliability makes it practically impossible to experimentally determine the lifetime of PICMA® actuators under real application conditions.
Therefore, tests under extreme load conditions are used to estimate the lifetime: Elevated atmospheric humidity and simultaneously high ambient temperatures and control voltages (Fig. 6).
Leakage Current
Leakage current measurements impressively demonstrate how effective the monolithic design of the PICMA® actuators prevents the penetration of moisture (Fig. 7).
The high insulation resistance of the PICMA® actuators remains stable over several time decades, whereas conventional polymer-coated actuators already exhibit a significantly increased leakage current after only a few hours.
Lifetime at Dynamic Continuous Operation (AC)
Cyclic loads with a rapidly alternating electrical field and high control voltages (typically >50 Hz; >50 V) are common conditions for applications such as valves or pumps. Piezo actuators can reach extremely high cycles-to-failure under these conditions.
Here, the most important factors affecting the lifetime of piezo actuators are electrical voltage and the signal shape. The impact of the humidity, on the other hand, is negligible because it is reduced locally by the self-heating of the piezo ceramic.
Suitable for Industrial Applications
Tests with very high control frequencies demonstrate the robustness of PICMA® piezo actuators. Preloaded PICMA® actuators, sized 5 mm × 5 mm × 36 mm, were operated at room temperature with compressed air cooling, with a sinusoidal signal of 120 V unipolar voltage at 1157 Hz, which equals 108 cycles daily. Even after 1010 working cycles there was not a single failure, and the actuators showed no significant changes in displacement.
Suitable for Use in Space
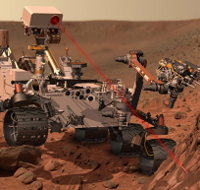
Performance and lifetime tests by NASA showed that PICMA® multilayer piezo actuators still achieved 96 % of their original displacement after 100 billion (1011) cycles. Therefore, they were chosen among a number of different piezo actuators for the science lab in the Mars rover "Curiosity".
>> PI Ceramic Supplies Piezo Actuators for Mars Rover Curiosity